“Innovation is in our DNA”
4 November 2024Left to right Bruce Carden, Stephan Becherand, Glen Harnett, Emily Schlegel, James Greenwood, Ben Pieyre and Troy Hand.
Article from Cranes and Lifting
For Ben Pieyre, CEO of BOOM Logistics and President of The Crane Industry Council of Australia, this was his second visit to the TRT Facility.
“I toured the facility two years ago and I was very pleased to see that Bruce Carden and his teams have implemented the developments they highlighted at that time. The quality of manufacturing is very high and includes ‘state of the art automation’ supported by skilled and experienced employees,” said Ben.
TRT’s site in Hamilton, New Zealand, is 33,000 square metres with 9,000 square metres under the roof line. In line with a recent board initiative to reduce the organisation’s carbon footprint, TRT has made significant strides in sustainability. Since Ben’s first visit, TRT has installed a comprehensive solar power system on two of its sheds, generating enough power to run all its machinery, plant, and equipment.
Currently, TRT has 600 kW of solar panels in operation, and once the project is complete, this will increase to nearly a megawatt at its head office and manufacturing facility.
With the current 600 kW setup, TRT is already reducing CO2 emissions by 50 tonnes annually, cutting their overall CO2 footprint by 44%.
Stephan Becherand, General Manager of Sales for Preston Hire was also on the tour.
“The warm welcome from the staff was a clear indication of TRT’s commitment to fostering strong relationships. The friendly and professional attitude of the employees set the tone for the day, making the visit both pleasant and informative.
“The tour of the factory was a journey through a world of innovation. The sight of cranes being assembled with precision was inspiring. The company’s commitment to utilising cutting-edge technology was evident in every corner of the facility. From state-of-the-art machinery to advanced design software, TRT is clearly at the forefront of technological advancement in the crane and transport industry. The engineering department is working very closely with their clients to ‘Make it Possible’,” said Stephan.
To continually improve its products, TRT’s management team has invested heavily in capital equipment and plant. These investments were made in brand new plasma cutting technology, enabling smarter cuts, cleaner cut lines and greater accuracy in their designs. There has also been significant investment in robot welding technology.
“When visiting the factory, you can follow the production and manufacturing process from the raw steel in the yard to the finished products – including the TIDD pick and carry crane, bespoke trailers and crane pads,” said Ben.
The investment in modern manufacturing technology is certainly a contributing factor to the build quality and the reliability of the product.
2023 saw significant improvements in manufacturing processes which are called ‘Drive Efficiency’. To drive greater efficiencies, TRT completely reorganised how it manufactures the TIDD pick and carry crane. This re-organisation has created a flow-on effect to the manufacturing processes, ensuring parts are handled in a timely manner and maintaining a high standard of work through visual control and Quality Assurance checks.
The factory manufactures two and a half to three TIDDs a month. They are built on a 14-week cycle and if a customer provides nine weeks’ notice, TRT will paint the TIDD on site in any two colours the customer wants.
“The investment in modern manufacturing technology is certainly a contributing factor to the build quality and the reliability of the product. I was also impressed with the culture and the level of skills and knowledge of employees. I experienced this when I interacted with various employees on the factory floor during my visit. Many have been with the family business for decades,” said Ben.
From the moment the factory receives and cuts the high-grade steel to ‘waving the mudflaps’ goodbye in the case of the TIDD, TRT manages all processes in- house. The steel is cut with new plasma technology and the factory has bending and press capabilities, where all the booms, the chassis and everything else are manufactured. All the major components are built in-house before going through to the new final assembly manufacturing facility.
“The innovation included in the new TIDD PC28-3G is impressive and I really look forward to seeing this crane in action. The visit to TRT was a testament to the company’s dedication to innovation, and sustainability. It was a glimpse into a company that is not just manufacturing cranes but is also shaping the future of the industry. The positive impressions from the visit reflect on a company that is poised for continued success and growth,” said Stephan.
TRT currently has 234 staff overall with 28 in the Australian business. Of the 234, 114 work in manufacturing.
TRT talks with pride about its people and its ‘Make it Possible’ culture. This attitude was apparent during the visit, said Ben.
“There was a positive attitude at all levels of the business, from Reception to the Research and Development team through to the factory floor. TRT organises a fortnightly meeting on innovation which no doubt drives the ‘can do’ attitude of the staff,” said Ben.
“It is clear there are also some exciting works in progress for the development of trailers and cranes. They use high quality design software and are able to tailor designs to accommodate and execute specific requirements for customers,” he said.
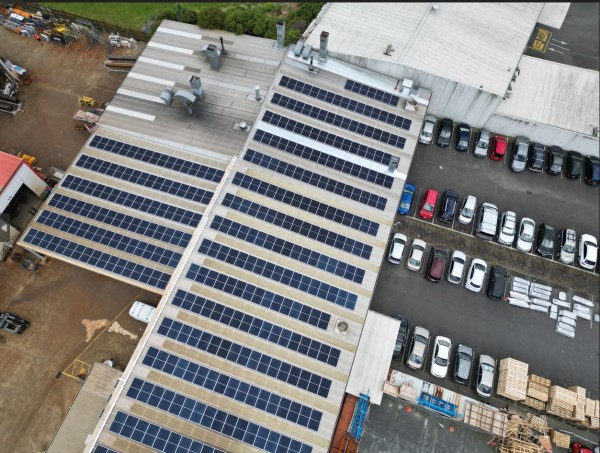
TRT recently installed a complete solar power system on one of its sheds from which it generates enough power to run all its machinery, plant and equipment.
TRT manufactures several products in the facility, including the TIDD pick and carry crane, bespoke crane trailers and crane pads. Ben was impressed with the new TIDD PC28-3G.
“The TIDD PC28-3G features a high level of technology with enhanced safety innovations and I was impressed with the high build quality of the product. Boom Logistics operates a fleet of TIDD pick and carry cranes as well as trailers designed and built by TRT. We are always focused on quality and innovation when choosing products for our fleet and for this reason, we would not dismiss consideration of any of the TRT products,” said Ben.
Crane and Lifting’s Emily Schlegel was also on the tour and had this to say.
“I wasn’t prepared for the enormity of the operation and the amount of innovative and ‘state of the art’ manufacturing technologies TRT has implemented to manufacture the TIDD pick and carry range, TRT bespoke trailers and TRT Crane Pads. It was fascinating to watch raw steel enter one door and a finished product roll out of another, out at the end of the manufacturing process,” she said.
“As a major manufacturer, TRT is focused on reducing its carbon footprint and has invested in a massive solar panel system that generates enough power for all manufacturing requirements. We were able to interact with personnel in the factory and everyone was extremely friendly and obviously passionate about what they do.
“The tour included a number of significantly influential individuals from the crane industry, and many had seen other Crane OEM manufacturing facilities around the world. The TRT facility compared favourably with anything they have seen. If you are given the opportunity to visit TRT, I strongly recommend you take it – you will not be disappointed,” said Emily.
Apart from manufacturing the TIDD, trailers and crane pads, TRT is proud to be the Kobelco Crawler Crane distributor for all of Oceania, covering Australia, NZ and the Pacific region. TRT is also the New Zealand and Queensland distributors of Manitowoc which includes Grove all terrains.
“Having known of TRT’s capabilities for many years, this visit was an eye opener to the dedication and abilities of everyone in the factory. Thank you again to Bruce and the TRT team for making the tour so enjoyable. TRT stands as a shining example of what can be achieved when innovation, excellence and a commitment to stakeholders and the environment are at the heart of a company’s ethos. The visit was a powerful reminder of the exciting possibilities that lie ahead in the world of crane manufacturing,” said Stephan.